
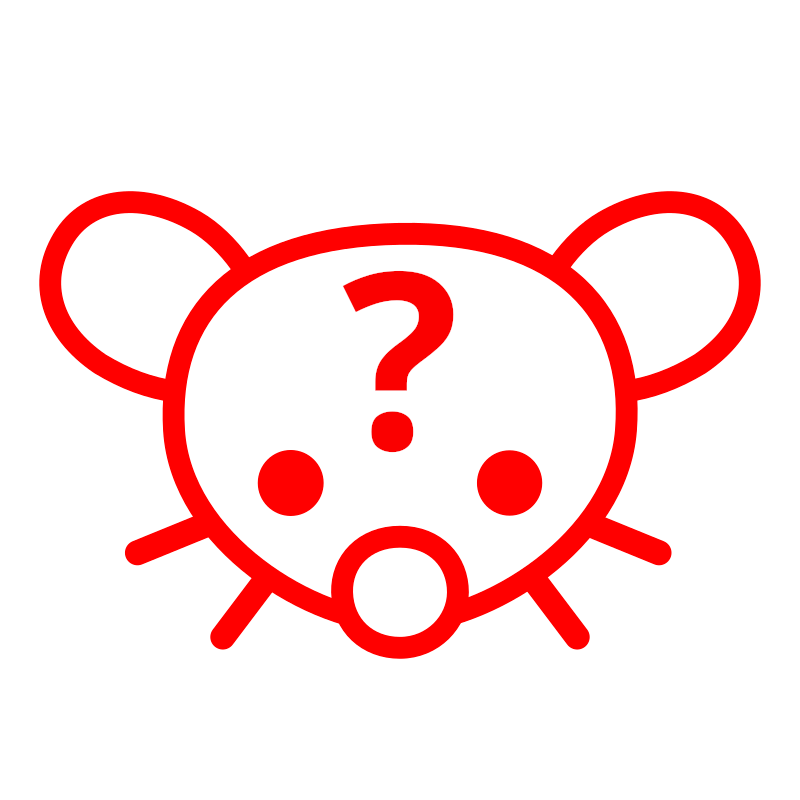
US, self employed (HVAC, family business) so if we don’t work, the business (and by extension, us) don’t make any money. That being said, we set our own schedule, so if we want to take time off, we can.
US, self employed (HVAC, family business) so if we don’t work, the business (and by extension, us) don’t make any money. That being said, we set our own schedule, so if we want to take time off, we can.
Fair point to some extent, but an electric speed controller (esc) is efficiency a software controlled switch anyway and thus is prone to the same manipulation. I suspect that this ‘software switch’ is nothing more than a flag telling the esc not to engage the motor.
Yeah, fair enough honestly
For just about any other case, I would say thats a great solution, but EUCs are self-balancing devices. A switch would be a potential failure point, and experiencing a power loss at speed would likely result in serious injury.
I have seen this done in a way that makes at least a bit of sense. My EUC (electric unicycle) came software locked to ensure that the motor didn’t engage if it somehow turned on during transit. Removing the lock required connecting it to the manufacturer’s app, but after that was done, I could use third party apps for everything else. Sure, there are other ways they could have done this, but this way ensures that the motor could not be engaged without human intervention.
A note on the Mercury wash station: despite being sold in a bundle with the Saturn 4 ultra, the build plate of the Saturn 4 series does not fit in the tub, so I would not recommend it for those printers.
I’m not very familiar with the lower end of index printers. Bambu does exist and seems to work well, but have no support for multimaterial flexibles, and I’m not a fan of the closed nature of their printers.
There are a few other solutions for single toolhead mmus, such as the prusa mmus and the ercf, but those have the problems you mentioned as well.
The only multi toolhead solutions I know of are on the high to very high end (Prusa XL, Voron Phoenix, and there are some projects for toolchangers and idex for the Voron 2.4).
Don’t forget the gold confetti
I’d go with 3d printing before welding. You can so quite a bit with a 3d printer and the CAD skill you gain are quite useful. I printed most of the parts for my 3lb robot and it heald up quite well.
I build and fight combat robots. Think Battlebots but smaller.
The reliability is largely dependent on how well it’s built. I have a 0.2 and a 2.4 and both have been quite reliable overall, but I did have some issues with my 2.4 recently where the frame came out of alignment (I didn’t tighten the screws enough when I built it), so my z axis belts became too loose. Assuming this will be the only capable printer you have access to, I would highly recommend printing spares of the more critical parts once you have it running. Otherwise, a catastrophic failure could lead to weeks of downtime while you try to source new parts.